Water atomizer device to optimize water and energy consumption
Water atomizer device to optimize water and energy consumption
Abstract
The water atomizer uses minimal electrical energy using a centrifugal fan to regulate the incoming air and compress it into a conical geometric shape, then combines the blown air with water droplets, accelerating them while converting them into smaller particles. Depending on the amount of water and the power of the fan, it can project water up to 200 meters and can be used in cooling and water supply systems for steel, cement, greenhouses, gardens, and wastewater treatment
Claims
The water atomizer device can optimize water and electricity consumption while creating a targeted range.
The atomizer device can accelerate water droplets by making them smaller and using the geometric shape of the nozzle by adjusting the inlet air pressure, and create a coverage area of water droplets up to 200 meters.
In this device, instead of current systems, using a fan as air supply and combining two conical nozzles with two different surfaces and sizes of cones and a certain curvature angle, and according to the formula A*V = Q and the ratio a1v1/a2v2 = q1/q2, while increasing the air launch speed in the second half of the cone, it converts or atomizes the water that enters the first cone into small droplets up to 5 microns when it collides with the air. In this case, due to the size and weight of the water particles, the gravity of the earth and its effect on the outgoing movement of the water particles are greatly reduced, and the atomized water particles can be launched at a maximum speed of 5 meters per second up to 200 meters.
1-2- The ability to create high velocity and very high numbers of water droplets with very little energy, as shown in
the table below, will increase water and energy efficiency in various industries by replacing the current system
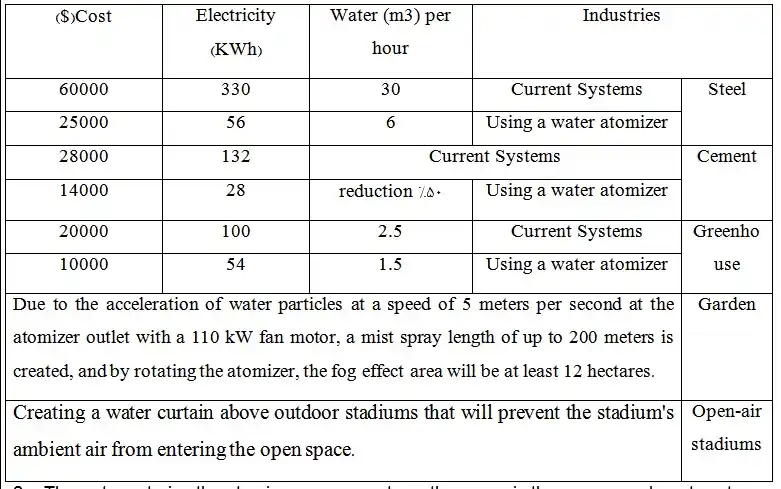
The water entering the atomizer can separate methane gas in the oxygen and wastewater mixing scheme in
industrial and municipal wastewater treatment.
Background Art
Many efforts have been made in the field of water atomizer nozzle production and they are used with applications such as dust control, for odor control, for crowd cooling, for mist production for aesthetic purposes, for snow making (EP1657509), for wetting bulk goods. In a similar patent, using a fan and blowing in a geometric shape exposed to water droplets with a high air inlet and using multiple atomizer heads at the outlet, they have claimed to use energy efficiently for use in the above-mentioned applications. (EP3081310) However, all these efforts have not led to the introduction of a significant milestone for improving efficiency and changing the way and amount of water used for large industrial applications with high added value. Also, the power of the device and energy consumption are not specified. This invention uses a centrifugal fan and uses a smaller geometric shape of the atomizer, especially compared to patent number EP3081310, due to wider applications in industries such as steel and cement, in agriculture such as greenhouses and gardens, and in urban and industrial purification facilities. Compared to all other examples, while using less electricity, it has more applications focusing on optimal water consumption and type of consumption. Also, depending on the power of electricity utilization, it can project atomized water droplets up to a distance of 200 meters.
Summary of Invention
In a water atomizer device, based on the use of a conical geometric shape with a difference in surface area and angle between the surfaces in the atomizer and the use of a centrifugal fan, by adjusting the inlet air and compressing it in a geometric shape and then combining the blown air with the pumped water droplets, while converting the water droplets into smaller particles and so-called water atomization, it is accelerated up to 5 microns. Considering the amount of water and the power of the fan, it is possible to throw fine water droplets up to 200 meters. The rotating motor under the device provides more spraying space. Also, this nozzle, using the least electrical energy compared to all nozzles used in industries, can eliminate the water sprinkler system used in the steel and cement industries that use compressed air for cooling, while reducing energy and saving water. In addition, in greenhouses, by creating fog and humidity and connecting it to a heat exchanger, the device controls the temperature and humidity of the greenhouse's interior, thus eliminating or using the greenhouse's internal fossil heaters in the shortest possible time. In a garden environment, due to the presence of a rotating motor under the nozzle and using the throwing power, it can create fog in 12 hectares of the garden, considering the 200-meter throwing radius of water droplets, and while regulating the air temperature of the garden, especially when we witness large changes in temperature during the seasons, it prevents product damage. Also, by using this device in the upper space of open-air stadiums and creating a water curtain, it prevents hot or cold air from entering the stadium space and creates an adjustable temperature in the stadium environment. The use of this type of atomizer in wastewater treatment can separate methane gas in the mixing plan and lead to the use of extracted gas for vehicle fuel. Also, due to low energy consumption, solar panels can be used to provide electricity. Finally, it has the ability to provide remote control, self-control, and alarm notification using smart electronic boards with the ability to connect to computers or mobile.
Technical Problem
High energy and water consumption in temperature change systems in industry is a major challenge. The amount and manner of this consumption in industry and agriculture can be considered the main point of crisis or advantage.
- Steel production industries
Periodic replacement of water nozzles due to expansion caused by the intensity and passage of water through the nozzle holes
The high diameter of water droplets in current cooling systems, which causes the heat transfer surface of these droplets with air to be low.
Water consumption per nozzle (1.89 cubic meters per hour). On average, there are 48 nozzles for each ingot production line in the steel industry, the consumption of which is 90 cubic meters per hour, which, taking into account the evaporation rate, is ultimately 30 cubic meters per hour, the non-renewable water consumption of each steel production line.
Considering the wind pressure created for the nozzle heads, which is 38 bar, each production line consumes 330 kWh of electricity (wind compressors).
- Cement production industries
Failure to achieve a temperature drop in cement production cooling towers from 400 degrees to 150 degrees (deviation of 20 to 50 degrees), which causes the electrofilters after the cooling tower to not be able to reduce NOX properly and will increase environmental pollution.
Failure of single and dual fluid nozzles due to water passage, which causes expansion and requires periodic replacement every 3 months.
- Greenhouse
High cost and energy share due to the use of fossil fuel heating systems in most greenhouses in cold and dry regions
High cost of providing high-efficiency heating systems
- Garden
Frostbite of gardens during the change of season, which destroys the crop or garden blooms.
Limited water resources in the use of modern garden irrigation systems
- Open-air stadiums
Negative impact of air and ambient temperature in open-air stadiums for holding sports competitions
Very high cost of using modern air conditioning systems in open-air stadiums
- Urban and industrial wastewater
Odor pollution
Very high capital requirement for purification and separation of methane gas for use as fuel
Solution to Problem
The use of atomized water droplets that have high range, optimal water and energy consumption can create efficiency in consumption by replacing current nozzle systems and other temperature supply systems. The use of a centrifugal fan and compression in a conical geometric shape and changing the pressure with the difference in surface area and angle between the surfaces in the atomizer and then combining the blown air with the pumped water droplets while converting the water droplets into smaller particles and the so-called atomization of water accelerates it up to 5 microns and, depending on the amount of water and the power of the wind thrown by the fan, allows the throwing of fine water droplets up to 200 meters. The atomizer material can include metals or polyesters, and it is more appropriate to use aluminum due to its lightness and machining ability.
- Steel production industry
Use of 4 water atomizers instead of the current 48 nozzles in steel ingot production
- Cement production industry
Replace 2 water atomizer nozzles with the current 8-stage nozzles
- Greenhouses
Eliminate internal heaters (with fossil fuel or electric) and water pipes and replace them with a
water atomizer nozzle with a rotating motor (the number of atomizers depends on the length and
width of the greenhouses) + an external heat exchanger (for heat supply) + a solar system for
electricity supply.
- Garden
Use a water atomizer with a rotating bottom motor for every 12 hectares, one device with the ability to connect to solar energy
- Open-air stadiums
Use 2 to 4 water atomizers (depending on the length and width of the stadium's open space) with the ability to rotate the bottom motor and use solar energy
- Urban and industrial wastewater treatment
Using an atomizer can separate methane gas at the outlet.
Advantageous Effects of Invention
- Steel production industry
No need to use current nozzles and consequently its maintenance and renovation costs
The cost of supplying and investing in atomizers is reduced by 50% compared to the current situation. (The cost price of each atomizer in mass production is close to $7,000, which is $25,000 for 4 devices, considering the connection and equipment, and the current 48-nozzle system is close to $60,000 ($50,000 purchase and $10,000 annual renovation and replacement costs).
The power consumption of the atomizer is 17% of the current consumption. (The energy consumption using 4 atomizers is a total of 56 kW for a production line (3 kW pump and 11 kW fan), and in comparison, the current nozzles require 330 kWh).
The water consumption in the atomizer is 20% of the current consumption. (6 cubic meters per hour for 4 atomizer nozzles that are The current ratio of 30 cubic meters is one fifth.)
Air compressors are eliminated.
Maintenance and stoppage costs due to nozzle failure are reduced. (The purchase cost of each nozzle is $150 and the cost of stopping production is very high)
- Cement production industry
Pressure pumps and single-fluid nozzles are eliminated in the cooling tower
The compressed air compressor for the two-fluid nozzle is eliminated.
Maintenance and stoppage costs due to nozzle failure are reduced.
Water consumption is reduced by 30 to 50 percent.
The atomizer in the cement industry consumes 20% of the current electricity consumption (the electricity consumption in the current system is 132 kWh and the atomizer system is 28 kW including the device and water pump)
Due to the appropriate 150-degree heat drop at the outlet of the cooling tower, the electrofilter operates properly and maximum NOX absorption occurs and negative environmental effects are greatly reduced.
A 50% reduction in investment in the cooling device (the cost of supplying atomizer devices (two atomizer devices) is $14,000 and the cost of the current system is $28,000).
- Greenhouses
Elimination of fossil fuels from the greenhouse product production process in replacement with solar energy
Elimination of thermal heaters inside the greenhouse, which have high energy costs and a high share in production costs.
Proper control of temperature and humidity in the greenhouse using a water atomizer
Elimination of water pipes in the greenhouse
50% reduction in investment in the cooling device (the cost of providing all equipment for each atomizer (including atomizer-electric exchanger-water source-electric panel and PLC-solar energy) is over 10 thousand dollars, and the cost of a pack of current modern heating systems is 20 to 25 thousand dollars).
Water in the atomizer is consumed 60% less than the current average (for each hectare of greenhouse, it is about 0.7 liters per second, which is 2.5 cubic meters per hour, and each atomizer nozzle is capable of consuming 1.5 cubic meters per hour (assuming one hectare of coverage).)
Electricity consumption with the atomizer is 60% of the use of current heating systems. (Energy is 14 kW for each atomizer device and about 20 to 40 kW for the heat exchanger, in contrast to and taking into account heat losses in greenhouses, which are usually between 50 and 150 watts per square meter (heater capacity (watts) = greenhouse area (2m) × heat losses (watts/m2)) for 10 thousand square meters, the amount is 100 kW for the current heater system)
- Garden
Preventing product loss during temperature changes Seasons
Helping garden irrigation based on a sprinkler system by creating fog and humidity in 12 hectares with one device
Eliminating drip irrigation system or other expensive water systems
Preventing soil compaction and erosion
Increasing yield by regulating garden humidity and temperature
- Open-air stadiums
Optimizing investment cost by replacing the atomizer device to create proper ventilation by eliminating expensive ventilation systems such as radiant coils (for cold regions) or cool wind systems
Using solar energy instead of fossil or electric energy in using water atomizer devices
- Wastewater treatment
Eliminating odor pollution from wastewater
Extracting methane gas from wastewater to use it as vehicle fuel
Industrial application
In the steel and cement industries, it acts as a substitute for current nozzles. In greenhouses, it acts as a temperature and humidity system. In gardens, it is used as a fogging device, a temperature and humidity controller for the garden, and as an aid in garden irrigation. In outdoor stadiums, it is used as a ventilation and temperature control system for the space of open-air stadiums, replacing current systems. In wastewater treatment, it is used as a methane gas separator to eliminate pollution and use it as fuel.
Patent Literature
WATER ATOMIZER WITH CONCAVE-CONVEX NOZZLE
This invention relates to water atomizers. More specifically, this invention relates to water atomizers which comprise a tubular nozzle with inlet and outlet. This invention further relates to a mobile unit which comprises a water atomizer, an energy source, a water pump, and a water tank. In addition, this invention relates to a method for the atomization of water.
Process and plant for making artificial snow
The method involves reproducing snow development conditions in upper atmosphere to reproduce in situ the artificial snow in an open autonomous enclosed space freed from external climatic conditions. A unidimensional flow is created at a temperature independent of the external temperature. A static pressure is created independent of the atmospheric pressure. The flakes transported by a stable gas layer are evacuated from the flow. An independent claim is also included for an installation for making artificial snow.
Non Patent Literature
Water and its consumption as an environmental material are of great importance in the cement and steel industries. In a case study in the cement industry, the water footprint of a factory in western Iran in 2017 was calculated to be 3,614,000 cubic meters, which indicates the high share of cement production in water consumption and the risk of the cement industry's survival in a landlocked country like Iran. Research has emphasized the use of equipment and solutions that can reduce water consumption in these industries, especially in areas where easy access to water is not available due to geographical location. Most efforts are devoted to finding solutions to reduce the water footprint, so that the equipment used and the impact of technology and its application for production in this industry have always had the greatest possible impact on reducing or increasing productivity. This impact on the production of various types of cement in cooling towers, where water is used to cool the product from 400 to 150 degrees, is of great importance for preventing environmental hazards. Also, the analysis shows that steel and pellet mills in a country like Iran need a fundamental review in the field of water resource management and improvement of water consumption and recycling processes. Cooling of steel in the outlet line and the use of the type of water consumed and the equipment used for spraying water are the main variables for this industry to optimize consumption. Most of the water sprayed for cooling steel evaporates and is considered a type of environmental loss, as in a study in a steelmaking site, about 90% of the water consumed evaporates (on average, 88% is drained from the water in an integrated plant and 94% in an EAF-based plant) and the need to use different methods for the equipment used in cooling has been tested, and the main condition for the advantage of these methods is the amount and effect of water consumption. In 2021, Mobarakeh Steel in Isfahan, Iran, consumed 27 million cubic meters of water, which accounted for about 5.5 percent of the total water consumption in Isfahan that year. Steel-producing industries also vary in their water consumption, depending on how old or up-to-date their machinery and equipment are. Given that steel-producing industries cannot operate without water, it is crucial to find innovative solutions to significantly manage the amount of water used in steel production. The steel industry is taking steps to reduce its water consumption and become more sustainable. By using newer technologies and adopting more efficient approaches to water management, the steel industry can help preserve this valuable resource for future generations.
Plants depend on water for growth, but many areas face water supply problems and have to spend a lot of money to benefit from water. Saving water in greenhouses is one of the ways to reduce costs. Water consumption in greenhouses is 61 percent less than in agricultural fields, and the reason for this is the reduction in the production cycle, the use of modern irrigation systems, and the reduction in evaporation. Of course, with all these conditions, the minimum amount of water required for greenhouse crops without a fan and pad system is 0.7 liters per second per hectare and with a fan and pad system, 1 liter per second per hectare. Naturally, given the limitations of Iran's water resources, only new and advanced systems should be used for irrigation. In arid and semi-arid regions of the world, which are faced with land and water constraints, various technologies such as cultivation type (vertical, hydroponic, aeroponic), greenhouse equipment, temperature, humidity and air control systems are used to save on inputs and energy. For example, vertical farming can be effective in increasing the efficiency of inputs per unit area. In closed vertical farming systems, water consumption is reduced by up to 95% and in some cases up to 99%, because the water used in the system is recycled and even water loss due to evaporation can be returned to the cycle by the dehumidification system. In a study conducted by Cecilia Stanghellini, various physiological and managerial components of agricultural water use efficiency have been revealed. And the potential improvements achieved by using greenhouses are analyzed. First, it has been shown that greenhouse producers usually have better tools for water management. It is then discussed how and why a greenhouse environment naturally leads to higher productivity and transpiration efficiency than growing in the field. Finally, the economic efficiency of water in greenhouses is determined. It is argued that this warrants investment in the infrastructure and tools needed to increase water use efficiency. Energy is also the next indicator in the cost of supply in greenhouses. The major part of production costs in greenhouses is related to energy and fuel. In a field study conducted in greenhouses in Mashhad, Iran, which aimed to determine the total energy required at different stages of production. As an example, greenhouse cucumber production and determining energy indices in greenhouses in the province were carried out. The results showed that a large part of the energy consumption (95.77%) in greenhouse cucumber production in Mashhad city is related to the fuel required for heating the greenhouse. Also, the energy ratio, net energy efficiency, and energy efficiency indices in greenhouse cucumber production in Mashhad city were obtained as 0.014, -6346470, and 0.025, respectively. Energy consumption in greenhouses in the studied region is very high, which, according to the review of the sources, is true in most greenhouses in Iran. The climatic characteristics of the regions (cold and dry) have made greenhouse temperature control difficult in the cold season and have caused the yield per unit area of the product to decrease in the cold season. This problem significantly reduces energy efficiency. Therefore, it is recommended to observe the practical principles of reducing energy loss in greenhouses and use high-efficiency heating systems.
One of the main problems for organizers of outdoor sports events is the impact of the external weather on the indoor atmosphere of outdoor stadiums, and as a result, the use of equipment that minimizes adverse environmental effects such as heat or cold. A case example of this was the FIFA World Cup games in Qatar, where all eight stadiums of the FIFA World Cup in 2022 benefited from modern and advanced air conditioning and cooling equipment. The ultra-advanced system installed in all stadiums, in addition to cooling the stadium space by pumping, also cleans and conditions the air in the stadiums, and this was done using solar energy from solar farms around Doha. The operation of this system was such that it first sucked the hot air from the environment and pulled it into huge chambers and cooled it using a cooling system installed there. Then the cooled air is completely cleaned using filters. Finally, this air is transferred to the entire space using very large fans and through vents installed everywhere in the stadium. The main problem with using these systems, apart from innovations and the use of solar energy to start up and provide its very high energy, is the cost of purchasing, installing and maintaining it, which makes many countries unable to use these systems to provide a suitable environmental space for their stadiums due to their cost. Nowadays, high-consumption systems such as flooding or low-consumption but expensive investment systems such as drip irrigation are used for garden irrigation. The main factor for creating efficiency in garden irrigation is paying attention to choosing the least expensive irrigation method and paying attention to methods of dealing with temperature changes during the change of seasons, which are two important challenges in maintaining products and garden space. The agricultural sector and its related activities have special characteristics that have made it highly exposed to numerous and unavoidable risks and damages. On the other hand, the range of occurrence of the aforementioned factors in the country is such that out of 40 types of natural disasters recorded in the world, 31 types can occur in Iran. (Malkoutikhah and Sokhte Sarai, 2010) On this basis, frostbite in agricultural products is ranked among the unexpected events that cause billions of dollars in annual losses to the Iranian economy (Omidvar and Dehghan Banadaki, 2012). In recent years, some experts have stated that modern irrigation systems have led to increased water consumption and reduced recharge of groundwater tables, and since they do not have a positive effect on the basin balance, they consider them to be inefficient activities. These critics state that modern irrigation methods do not actually save water. They believe that the water flowing out of the field and the water that has infiltrated into the ground are not losses and can be used in some way.
The presence of organic matter, aerobic and anaerobic bacteria, and the numerous chemical and biological interactions that occur between them ultimately lead to the production of various gases such as hydrogen sulfide and ammonia, methane and other volatile cyclic compounds, and septic gases. The release of these gases from sewage wells and their dispersion in residential and industrial environments and nature not only causes a foul odor in the air, but also severely damages the respiratory system. Energy production from urban wastewater is one of the types of conversion energies that, with the increase in urban population on the one hand and the expansion of industries on the other, the issue of environmental pollution is becoming more important day by day. One of the most important issues in the field of environmental health is how to treat urban and rural wastewater and prevent the entry and penetration of these pollutants into water and soil. Untreated wastewater is one of the pollutants that contains large amounts of biodegradable organic matter and pollutants, numerous pathogenic microorganisms and toxic compounds. There are various methods for producing energy from wastewater, such as biogas treatment plants.
In this method, wastewater is transported to a treatment plant where it is decomposed by microbes. During this process, biogas gas is produced, which includes methane (CH4). This biogas can be used as an energy source to produce electricity or heat.
References
- Alireza Kiani, Study on the Effectiveness of Modern Pressure Irrigation Systems in Iran, Journal: Water Management in Agriculture, 2021
- Bazrafshan Javad et al., Documentary analysis of modern irrigation and agricultural water technologies in the world and the possibility of their localization in Iran, Journal of Strategic Research in Agricultural Sciences and Natural Resources Volume 7, Issue 2, Pages 139 to 158: 2022
- Bahadori, Babak, Resource management and water consumption pattern reform in the mining and mineral industries sector of Iran, Majles Research Center, 2019
- Cecilia Stanghellini, Horticultural production in greenhouses: Efficient use of water, Wageningen University & Research, 2014
- Dheeraj Chouhan, Role of Water Temperature in a Spray Cooling of a Hot Steel Plate at Different Initial Temperatures, National Institute of Technology, Rourkela, 2016
- Hosseinian Seyed Mehdi, Model for calculating the water footprint of cement production with the approach of reducing water consumption through optimizing energy consumption (a case study in western Iran), Journal: Sharif Civil Engineering: 2019 | Volume: 35-2 | Issue: 3/1 Pages: 123-133
- Mohammad Hossein Saeedi Ard, Study on Energy Consumption in Greenhouse Cucumber Production (Case Study - Mashhad City), Greenhouse Vegetable Promotion Magazine, Volume 7, Issue 1, 2024
- Patents No. EP1657509 & EP3081310
- Report of the Ministry of Industry, Mines and Trade of Iran on the Critical Water Situation in the Steel Industries of Iran, 2021
- Sanjabi, Samaneh, Dealing with frost damage of garden crops; A Necessary and Planning-Requiring Solution to Achieve a Green Economy, 2016