تحلیل سیستم غبارگیر مجتمع ذوب شهریار با استفاده از دینامیک سیالات محاسباتی (CFD) و بررسی پارامترهای موثر در فرآیند دداستینگ و افزایش عملکرد آن
تحلیل سیستم غبارگیر مجتمع ذوب شهریار با استفاده از دینامیک سیالات محاسباتی (CFD)
و بررسی پارامترهای موثر در فرآیند دداستینگ و افزایش عملکرد آن
امیر زائرین _حسین ستارنژاد
شرکت مجتمع فولاد صنعت بناب
چکیده
سیستم غبارگیر فولادسازی به عنوان ریه های تنفسی کارخانه است که عملکرد صحیح آن تاثیر چشمگیری در حذف غبار و آلودگیهای هوای ناشی از فرآیندهای تولید و درنتیجه حفظ سلامت کارکنان زحمتکش فولاد مجتمع فولاد صعنت بناب و همچنین محیط زیست دارد.
شرکت مجتمع فولاد صنعت بناب ، بعنوان یکی از تولیدکنندگان محصولات فولادی استاندارد، با اتخاذ استراتژی تولید سبز، نسبت به حفظ سلامت نیروی انسانی شاغل، کاهش میزان آلودگی ها به منظور استفاده بهینه و با حداکثر راندمان سیستم موجود و همچنین جلوگیری از مصرف زیاد انرژی و از همه مهمتر رهایی از مشکلات آلایندگی در حین فرآیند تولید ،کارشناسان واحد مهندسی با استفاده از طراحی و تحلیل جریان سیال با استفاده از برنامه انسیس فلوئینت (CFD) تغییر در جانمایی سیستم فیلتراسیون دستگاه غبار گیر و بهینه سازی هودهای کوره ذوب القایی شهریار جهت رفع مشکلات افت فشار دستگاه هواکش بازنگری صورت گرفت.
واژه های کلیدی: سیستم غبارگیر، راندمان ، طراحی داکت کشی،آنالیز جریان سیال (CFD)
مقدمه
تکنولوژی نوین، با بکارگیری مهندسی مکانیک و مهندسی برق در راستای تولید محصولات فولادی با کمترین آلودگی زیست محیطی گام بر می دارد. در تولید هر تن از محصولات فولادی بین 10 الی 25 کیلو گرم گرد و غبار ایجاد می شود، بی شک سیستم های غبار گیری پیشرفته در صنعت مدرن حائز اهمیت هستند، اما هزینه ها و مبلغ سرمایه گذاری شده برای این فرآیند نمی بایست بالاتر از حدانتظار صاحبان صنایع باشد.
توسعه صنعتی و پیشرفت تکنولوژی دستاوردهای متنوعی را به زندگی انسان ارائه نموده است. در روند پیشرفت واجرای برنامه های توسعه صنعتی پس ماندهایی به شکل ترکیباتی نا خواسته واغلب زیان آور به محیط رها میشوند به گونه ای که اثرات منفی بسیاری بر محیط زیست می گذارند. پدیده آلودگی هوا نیز یکی از ره آوردهای توسعه صنعتی است که با افزایش جمعیت و گسترش شهر نشینی و مصرف بیشتر سوخت های فسیلی بر شدت آن هر روز افزوده می شود.
طبق مشخصات فنی موجود سیستم غبار گیر ذوب کوره های القایی ، با ظرفیت فیلتراسیون دو دستگاه فن غبارگیر با مشخصات 225000 مترمعکب در ساعت بوده که با توجه به تعداد کیسه فیلترهای در نظر گرفته شده، به دلیل عدم طراحی مناسب داکتهامقدار مکش دستگاه های هواکش با افت فشار مواجه بوده و پس از نصب و راه اندازی عملا مقدار پیش بینی شده حاصل نشده است.
بررسی پارامترهای موثر در راندمان سیستم غبارگیر کوره های القایی
سطح فیلتراسیون : تعداد فیلترهای در نظر گرفته شده در سیستم فعلی، 2432 عدد با ابعاد L4000*Ø160می باشد که با توجه به محاسبات انجام گرفته در خصوص Filtration surface[1] و در نظر گرفتن قدرت مکش فن بمیزان 450000 مترمکعب در ساعت، برای دو دستگاه هواکش فن ، حدود 6300 متر مربع سطح فیلتراسیون لازم است در حالیکه مقدار سطح فیلتراسیون موجود حدود 5000 مترمربع میباشد، بنابراین سطح فیلتراسیون موجود کمتر از مقدار نیاز است.
[1] SF=0.014 .Q
پارامترهای مختلف طراحی دداستینگ:
1- توزیع یکنواخت جریان مکش هوا در هودهای طراحی شده
2- ارتفاع هودها از سطح کوره ها و دهانه هودها
3- طراحی صحیح قیف و لبه های هودها
4- میزان افت فشار و در نتیجه مکش فن
5- طراحی مناسب داکت ها
6- طراحی هود مکش کوره
7- افت فشار استاتیک
8- مکش دود و غبار کوره ها در همه حال و حتی در زمان شارژ مواد
5- خنک نمودن هوای ورودی به سیستم غبارگیر و جلوگیری از آتش سوزی فیلترها
6- کاهش هزینه های نگهداری و تعمیرات مربوط به تعمیر و تعویض داکت ها و هود ها
باز طراحی هودها و داکت ها و محاسبات مربوطه با اعمال شرایط بهینه موثر برفرآیند اصلاحات موردی در قطر داکتها برای افزایش راندمان در جهت توزیع یکنواخت جریان مکش در ادامه اشاره شده است.
تحلیل با نرم افزار Ansys Fluent
در بررسی های آنالیز شبیه سازی جریان سیال با استفاده از نرم افزار فلوئنت، شبیه سازی تحت شرایط مشخصی انجام گرفته که یکی برای سیستم با قطر داکت قبل از تغییرات هندسی با مشخص (d1=850 , d2= 1050) که بعد از شبیه سازی جریان سیال نتایج بدست آمده، میزان افت فشار در این سیستم به حداقل ممکن رسیده است.میزان دبی مورد نیاز پیشنهاد شده برای جمع آوری داست کوره طبق محاسبات انجام گرفته و استاندارد(VS -55 -03) ACGIH برابر با CFM) 2500)
مطالعه، برای کوره القایی 20 تن، مقدار دبی مورد نیاز مکشm3/hr 85000 خواهد بود. طبق استاندارد( VS-55 -07) بایستی توجه داشت که سرعت مکشی جهت ربایش آلاینده ها حداقل m/s 18 در نظر گرفته میشود.
Duct of Furnace A:
Q = V. A
Q = Air or Gas Flow (m3/hr)
V = Transport Velocity in Duct (m/s)
A = Round Area of Duct (m2)
Q1 = Area x velocity = 85,000 m3/hr = area x V (18 m/s)
1292 =D1
Duct of Furnace B:
Q = V. A
= 1780 mmD2
انجام محاسبات بالا درخصوص انتخاب قطر داکتهای موردنظر، باپیشنهادتغییر جانمایی سیستم داکت کشی بشکل شماره (1) زیر ارایه گردید

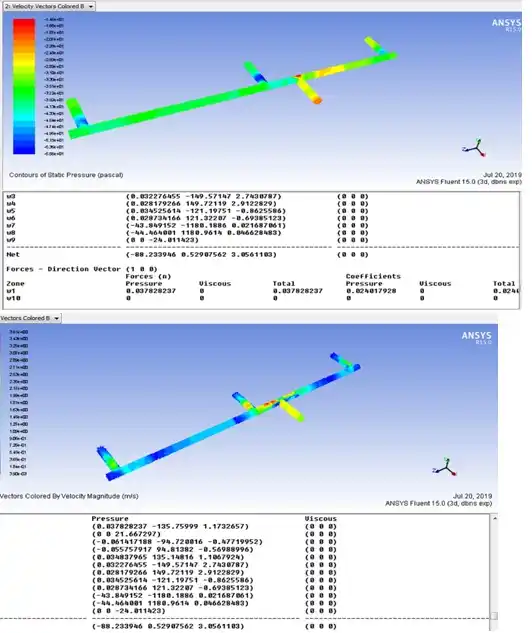